Process Planning
- Home
- Solutions
- Manufacturing
- Process Planning
Process Planning
In the domain of Process-Methods Engineering, proficiency in project management, automotive knowledge, and a deep understanding of advanced automated systems are essential. The primary objective is to anticipate upcoming digital shifts and develop effective implementation strategies.
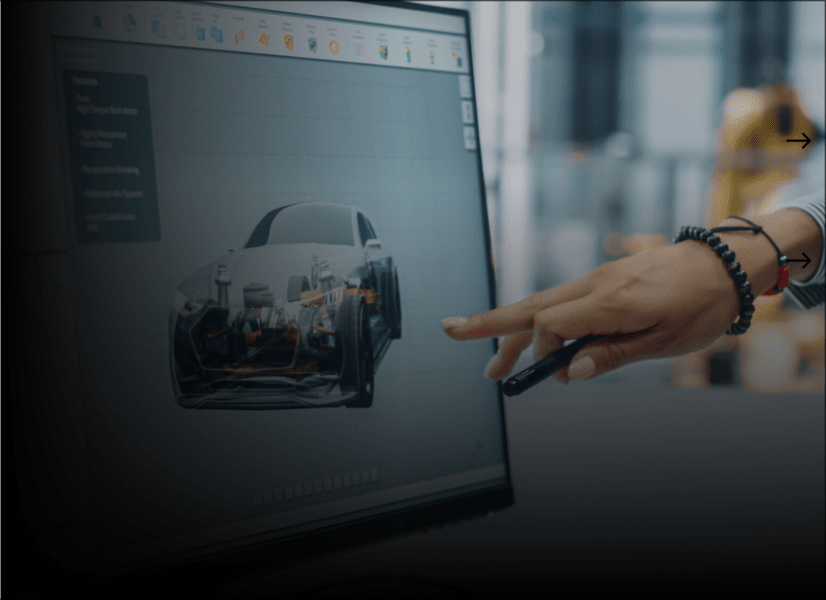
Acting as a crucial intermediary between project management and production, professionals in this field optimize existing production systems for large-scale production in new projects. They provide the development team with insights into efficiency, product durability, and time-to-market considerations. Additionally, they contribute to defining business requirements and devising optimal solutions aligned with future needs. Their overarching mission is to anticipate future trends in digital transformation and capitalize on the opportunities they present.
Within Manufacturing Engineering, automotive OEMs and their suppliers face relentless pressure to cut costs and streamline cycle times. Understanding this challenge, G Square Techsystems offers comprehensive support to help customers achieve productivity gains and cost reductions.
Our engineers possess diverse skills in manufacturing, including:
Within Manufacturing Engineering, automotive OEMs and their suppliers face relentless pressure to cut costs and streamline cycle times. Understanding this challenge, G Square Techsystems offers comprehensive support to help customers achieve productivity gains and cost reductions.
Our engineers possess diverse skills in manufacturing, including:
Manufacturing Engineer DPA5:
Desired Profile: Responsible for assessing final assembly manufacturing feasibility, planning, and supporting program implementation. Works closely with cross-functional teams such as Product Design Engineering, Facility, MP&L, and Plant Engineering to validate design and assembly feasibility for new product launches. Identifies opportunities for cost savings in assembly, labor, and tooling.
ECU Software Validation:
Experience: Overseeing the entire Software Development Life Cycle (SDLC), including managing requirements, design, development, estimation, planning, implementation, and quality assurance. Responsibilities include preparing test plans covering DV / PV tests, functional verification, testing at various levels (SIL, MIL, HIL, bench, system, and vehicle), test process automation, and conducting environmental and EMI EMC tests, including UDS protocol.
Overview:
During the early stages of the design phase, rapid feasibility studies and risk analyses are conducted to swiftly assess new concepts. The objective is to identify risks and potential issues early on, explore various design solutions, and evaluate the impact of design changes. Product concept evaluation plays a crucial role in this process.
Engineering Change Management:
The Engineering Change Management process involves requesting, determining feasibility, planning, implementing, and evaluating changes to Engineering Products. Its goals are to enable a systematic and controlled change process and ensure traceability of changes through proper execution.
Manufacturing Process Planning:
Manufacturing process planning is a comprehensive approach that integrates the management of manufacturing data, operations, and PLM processes to optimize production cycles for efficiency and speed. This methodology empowers business teams to strategize, simulate, and refine manufacturing processes and product designs before final production begins.
The production process encompasses various stages, including operation sequencing, machine process planning, assembly line planning, and communication within the organization and with external partners. Manufacturing companies are continuously seeking innovative technologies and methodologies to develop and integrate high-performing processes, ensuring they maintain a competitive edge. These firms often decentralize process manufacturing across multiple plants and suppliers located in different geographical regions.
Effective production processes require continuous monitoring, traditionally facilitated by ERP systems or computerized process plans. However, these solutions may lack scalability and extensibility. Consequently, many businesses are transitioning to Manufacturing Process Planning (MPP) software, which supports engineers in designing and developing products and manufacturing processes concurrently.
Looking ahead, let’s delve deeper into the functionality of manufacturing process planning and explore the advantages of utilizing MPP software to manage manufacturing information.
The production process encompasses various stages, including operation sequencing, machine process planning, assembly line planning, and communication within the organization and with external partners. Manufacturing companies are continuously seeking innovative technologies and methodologies to develop and integrate high-performing processes, ensuring they maintain a competitive edge. These firms often decentralize process manufacturing across multiple plants and suppliers located in different geographical regions.
Effective production processes require continuous monitoring, traditionally facilitated by ERP systems or computerized process plans. However, these solutions may lack scalability and extensibility. Consequently, many businesses are transitioning to Manufacturing Process Planning (MPP) software, which supports engineers in designing and developing products and manufacturing processes concurrently.
Looking ahead, let’s delve deeper into the functionality of manufacturing process planning and explore the advantages of utilizing MPP software to manage manufacturing information.