DFMEA / PFMEA Studies
- Home
- Solutions
- Manufacturing
- DFMEA / PFMEA Studies
DFMEA / PFMEA Studies
Failure Mode and Effects Analysis (FMEA) is an essential analytical tool utilized across various fields to ensure comprehensive consideration and resolution of potential issues throughout product and process development. PFMEA (Process Failure Mode and Effects Analysis) focuses on manufacturing processes, while DFMEA (Design Failure Mode and Effects Analysis) targets the product design phases. This method emphasizes risk assessment, fostering discussions on design, function review, application changes, and potential risks of failure.
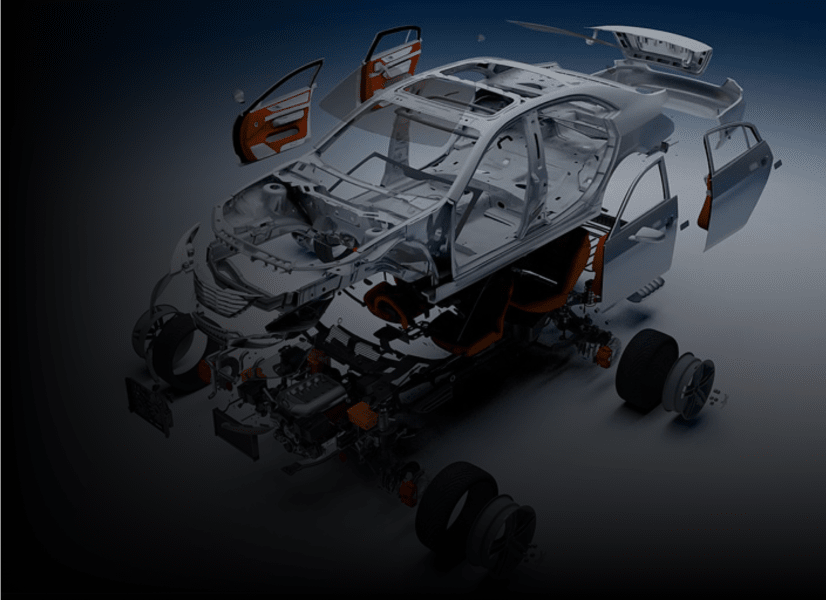
The team at G Square Techsystems possesses extensive experience in developing and refining Process FMEA. Inputs considered for PFMEA include:
PFMEA involves collaboration among cross-functional teams, including Manufacturing, Product Process, and Quality experts. In some cases, safety engineers, customer representatives, and supplier teams are also involved. PFMEA analysis extends to both assembly and individual component-level manufacturing processes. Potential effects are systematically identified, considering attributes like noise, poor appearance, safety risks, loss of primary function, performance issues, and their impacts on end-users due to failure modes such as assembly difficulties, tapping or boring failures, and operator safety concerns. Similarly, potential causes are identified concerning equipment, including tool wear, inadequate clamping, worn locators, broken tools, gauging inaccuracies, and operator errors such as incorrect part selection, improper tooling, wrong feed or speed rates, and mishandling.
Process Controls are recommended, encompassing preventive measures like operator training, statistical process control (SPC), inspection verification, work instructions, maintenance protocols, error-proofing through design, and detective methods like functional testing, visual inspection, gauging, and final testing. Each parameter is categorized according to customer organization standards into key, fit, or function, and safety-critical characteristics for control methodology.
Process Controls are recommended, encompassing preventive measures like operator training, statistical process control (SPC), inspection verification, work instructions, maintenance protocols, error-proofing through design, and detective methods like functional testing, visual inspection, gauging, and final testing. Each parameter is categorized according to customer organization standards into key, fit, or function, and safety-critical characteristics for control methodology.
Key Steps for Conducting a Successful PFMEA Session:
1. Select an Effective Facilitator:
Choose a facilitator who can keep the session on track. Teams often spend too much time debating Severity, Occurrence, and Detection values, which can hinder progress and deter future participation. When in doubt, opt for higher values, emphasizing risk assessment and the implementation of countermeasures.
2. Leverage Engineering Expertise:
Involve both design and process engineers in the PFMEA session. Design engineers can offer insights into Severity levels, while process engineers can assist in evaluating occurrence and detection levels, enhancing the overall analysis.
3. Clarify Evaluation Criteria:
Distribute hard copies of the Severity, Occurrence, and Detection criteria at the beginning of the meeting to ensure everyone understands the assessment parameters. Reviewing these criteria with the team helps maintain consistency and understanding throughout the session.
4. Utilize Process Flow Diagrams:
Ensure a comprehensive Process Flow Diagram is prepared before the PFMEA session begins. This visual aid helps participants grasp the sequence of steps and identify potential failure points more effectively.
5. Prioritize Risk:
Sort the PFMEA spreadsheet by Risk Priority Number (RPN) in descending order by the end of the session. Allocate time to brainstorm and devise countermeasures for high RPN values. Many organizations set maximum allowable RPN thresholds for processes, mandating the implementation of robust countermeasures by process development or Six Sigma teams.
6. Include Countermeasure Planning:
Add additional columns to the PFMEA spreadsheet to document planned countermeasures and their expected impact on risk levels. This proactive approach ensures that risks are mitigated effectively, leading to improved process reliability.
7. Maintain as a Dynamic Document:
Treat the PFMEA as a dynamic, “living document” that requires regular updates. As knowledge evolves and additional insights are gained regarding true Severity-Occurrence-Detection values and countermeasure effectiveness, revise the PFMEA accordingly to reflect the latest information.